Our Ghent plant continues its pioneering role in our electrification
Let’s learn more about the challenges of, within a year from now, tripling the electric car building capacity in our Ghent plant to 135,000 vehicles.
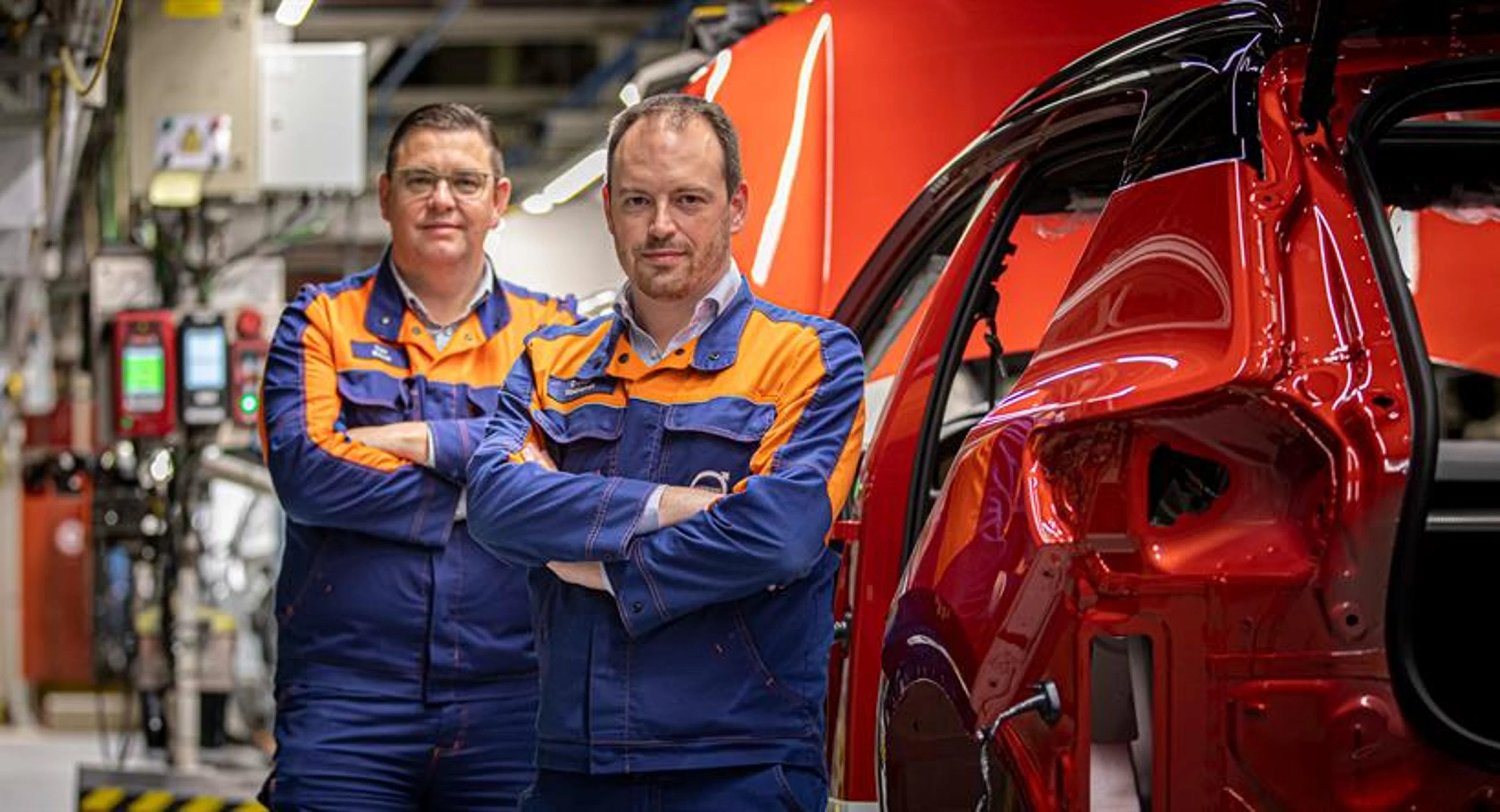
Tom Buyse (left) and Dieter Roelandt are working with rebalancing activities in the Ghent plant.
Our Volvo Cars Ghent plant became the first site in our manufacturing ecosystem with a battery assembly line when we introduced our first pure electric car model, the Volvo XC40 Recharge. Now, the launch of our new Volvo C40 Recharge pure electric SUV underscores the Belgian plant's role as a trailblazer on our electrification journey.
We talked to a couple of our team members in Ghent to get a better understanding of the ongoing rebalancing act – which involves optimising operations and machine time to match the desired production rate.
"The big challenge is to make our processes more efficient," says superintendent Tom Buyse, who is closely involved in rebalancing stations in the C-shop. "This is done mainly through activities within the three Kaizen* areas of Muri (unevenness), Mura (overburden) and Muda (waste). Focus is mainly on eliminating abnormalities and optimising working conditions for the operators."
Tom continues: "A rebalancing of this size is also a unique opportunity to change the structure of our processes, starting from scratch. Just because an assembly activity has been done in a certain area for decades, it doesn't mean it has to stay there forever. By moving activities forward or backward in our processes, we can solve quality issues."
“A rebalancing of this size is also a unique opportunity to change the structure of our processes, starting from scratch.”
To utilise this unique opportunity to change the structure of the process, the teams can for example think of a metal car body and ask questions like: What is the most logical way to turn the body into a finished car? In what order should the assembly activities be done? What is the most logical place for each activity? Which is the most ergonomic assembly approach to ensure a safe and healthy work environment? And so on.
Dieter Roelandt works as a supervisor at pre-trim. He has spent much of his time doing this exercise together with the team leaders of his area.
"This way of thinking helps us draw the lines and determine which of the teams is most suitable for each assembly activity," Dieter says. "It's very exciting. We have a unique opportunity to rethink and optimise our work by reinforcing the culture of continuous improvement."
As the number of jobs per hour and the production volume increase, Volvo Car Ghent is in the process of recruiting 500 new employees, mainly production workers.
Dieter concludes: "It feels fantastic to contribute to the transformation and growth of our company by reinventing the way we work and welcoming new colleagues on board."