Story
How a terminal plays a leading role in Volvo's circular ambitions
Volvo Cars aims to become a circular business by 2040 to cut its climate and biodiversity impact, create new value, and build resilience. A terminal in Maastricht plays a key role in this ambition.
Fleet
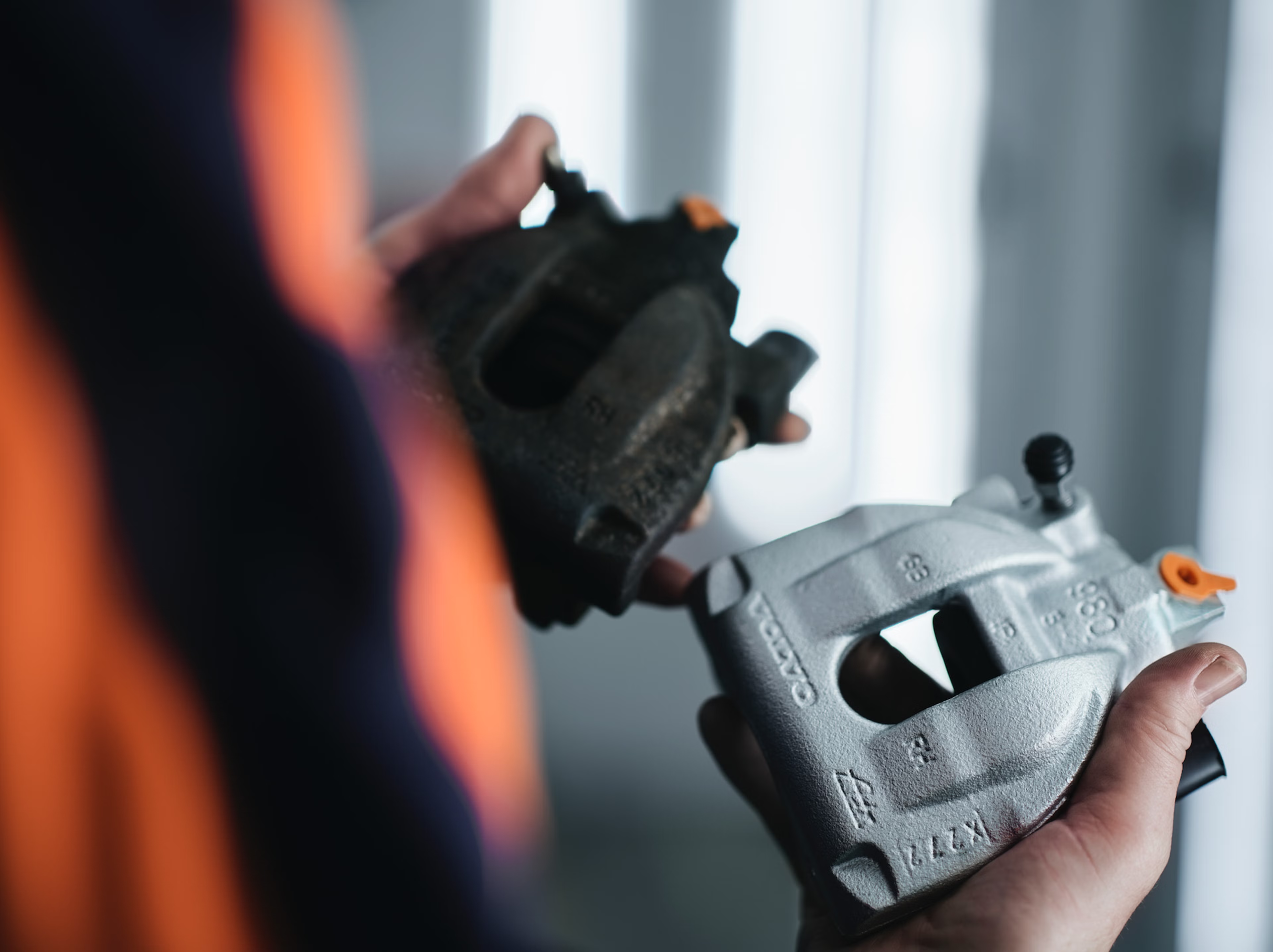
The Exchange Terminal Maastricht extends the life of parts, giving them a second life and reducing waste.
Explore our Sustainability pagesExtending the life of parts
In Maastricht, we have a facility that plays a key role in our circular goals and leading to a profitable way to reduce carbon from spare parts placed on the market. It is our hub for collecting used parts before they are remanufactured back to as good as new quality, or better.
Remanufacturing is crucial in the circular economy, where raw materials are reused after a product's life cycle. The Exchange Terminal Maastricht (ETM) extends the life of parts replaced by Volvo Cars retailers. Used parts from around the world are sent to this terminal, where they are identified, stored, recycled, or sent to remanufacturers. After remanufacturing, the parts are sent to our customers via retailers.
Creating the infinite loop
Producing new parts will, in general, consume more resources than remanufacturing existing parts. Reuse also reduces waste and gives parts a second life. By keeping the process in-house, we can continue to supply high-quality parts for existing models for a longer period, meeting our high standards.
“When a part comes to us and is found suitable, it is stored in our warehouse. It is not sent directly to the remanufacturer unless necessary. This could be tomorrow, a year from now, five years from now, or even fifteen years from now. We are unique in this,” says Raymond Huveneers, Group Manager at ETM.
"It is a closed system from Volvo Cars. This enables us to truly work with circularity, keeping materials in an infinite loop."
| Mirjam van der Zanden, Facility Manager at ETM
If a part does not meet our quality requirements, it is recycled. “It is important that the transports of the parts that are recycled are sealed. This ensures that the load actually ends up at the recycling company and goes directly through the shredder,” says Mirjam van der Zanden, Facility Manager at ETM. “It is a closed system from Volvo Cars. This way, we can accurately track how many kilos of steel, copper, plastic, and other materials are collected, removed, and recycled. This enables us to truly work with circularity, keeping materials in an infinite loop.”
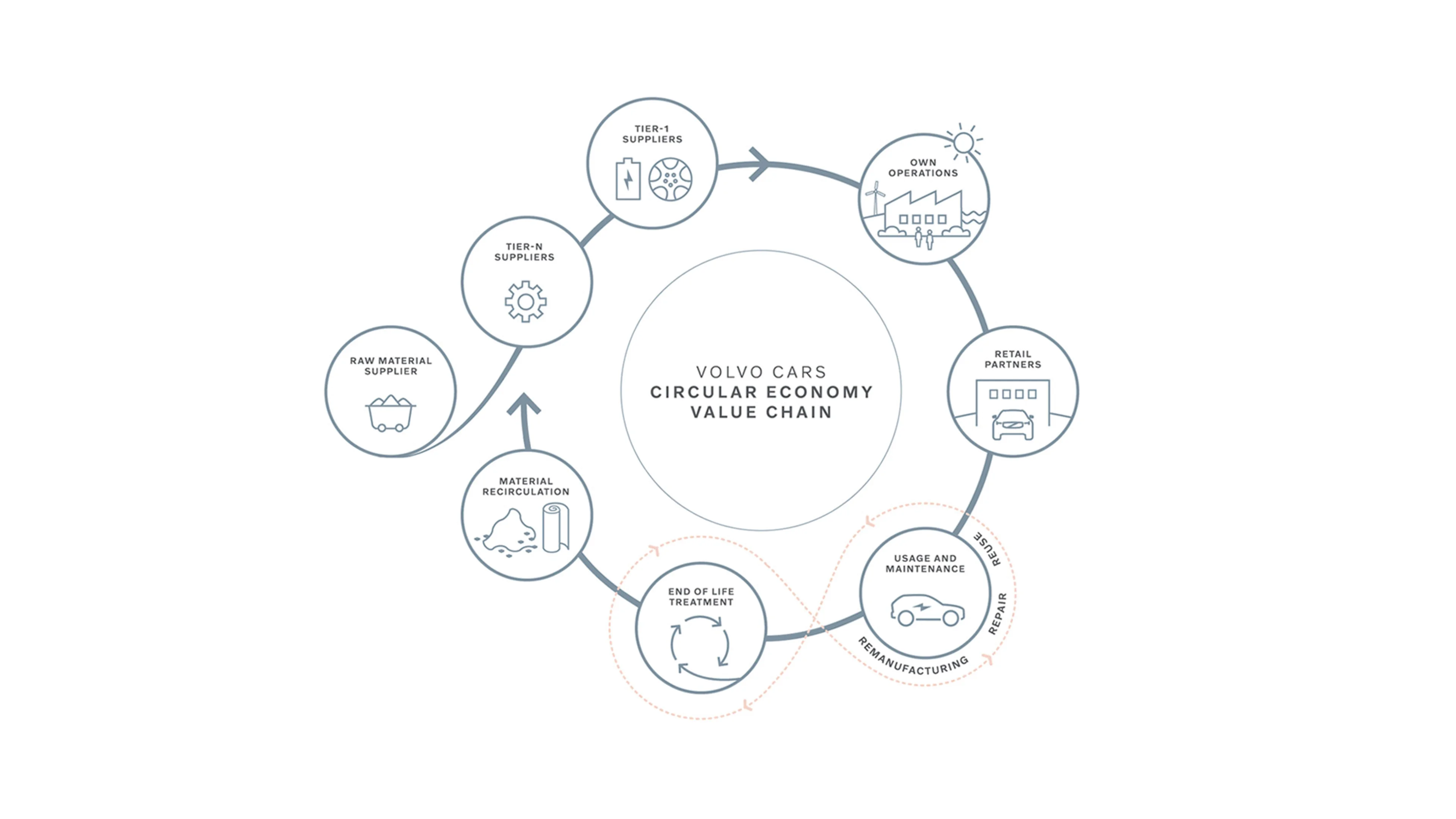
Volvo Cars circular economy value chain
Why not recycle everything?
The advantage of remanufacturing is that it can extend the lifespan of the part, reduce environmental impact, and provide customers with high-quality parts equal to a newly produced one. This process saves us approximately 85% of raw materials and uses 80% less energy compared to producing new parts, resulting in significant CO₂ and cost savings.
From history to the future
The Exchange Terminal Maastricht started in 1995 in Born when the Volvo S40 went into production. “We started with a handful of employees in a small building with 5,000 parts in stock. Few believed in its future, but Volvo Cars had foresight. Look where we are now,” says Mirjam.
The ETM has achieved remarkable milestones in supporting a circular economy, handling hundreds of thousands of cores per year, recycling waste into valuable material, and sending parts to remanufacturers for reuse. By the end of 2024, the terminal held over 1,000,000 cores in stock. The operation involves collaboration with 18 remanufacturers across eight countries, showcasing a global commitment to sustainability and resource efficiency.
“Despite significant growth in recent decades, we are only at the beginning of the circular economy. We are running pilots with reuse as a supplement to remanufacturing, repair, and recycling. We use point systems for retailers who send parts to us, involving retailers and certified repairers even more to ensure an optimal circular system,” concludes Raymond.